
Kent Towers | Ottawa
See The Collaboration
Kent Towers
Ottawa, Ontario
Project Consultant: WSP Ottawa
Glazing Subcontractor: Fendor Glass & Aluminum
Major metropolitan areas like Toronto and Ottawa saw a large multi-family apartment construction boom in the 1960’s and 70’s. The majority (60%) of building permits issued in Canada from 1962 to 1973 were for multi-family dwellings, making these buildings more than 50 years old today.
As many of the systems and products come to the end of their useful life, condo and apartment management boards look for opportunities to improve performance and add value to tenants. Window replacement is a crucial opportunity to upgrade the performance of the envelope, improving thermal performance with triple glazing, low-emissivity (low-e) coatings and a variety of thermal break technologies. These improvements support the reduction of heating and cooling requirements, and importantly, lower expenses for residents.
Kent Towers in Ottawa is a great example of a 1970’s era building with windows that had reached the end of their useful life. Showing performance failures with air and water leakage, the board engaged WSP to conduct a full assessment of the windows and identify whether a retrofit, involving new insulating glass units, would be viable or whether a window replacement would be the best investment for performance, durability, and payback.
“During the refurbishment evaluation, we did frost point testing for the IGU to see if they were still viable, but they didn’t perform well, and they were also coming close to the end of their useful life, so we wanted to provide a solution that was durable long-term for the building and residents,” said Jean-Phillipe Caux, Project Director at WSP.
The WSP team worked closely with OBE during the design phase of the project to assess the viability, performance, and durability of different solutions.
“Our OBE rep was always available and very responsive during the design and assessment phase of the project as we explored options together. He sent us sketches and dimensions to assess sizes and design solutions and provided details that we could share with the condo board,” noted Caux.
With a goal of eliminating leaks and providing a viable, long-term solution for the board and tenants, the team selected the OBE 1250 Arctic Slider window as the primary solution, using an insulating glass unit as the outboard lite and single pane of glass as the inboard lite. A triple glazed slider would give the owners exceptional thermal performance and still maintain the function and aesthetic of a sliding window.
“We’ve used OBE’s 1250 Arctic Slider window on several projects,” said Kurt Westwell, senior vice president at Fendor, the glazing contractor on the project. “We’re really familiar with them and it’s a better product than others in the market.”
“Older slider windows are usually very large, so size limitations pose challenges for replacement projects. The Kent Towers had sliders over fixed windows, so we worked with OBE to provide a solution to meet the design requirements,” said Caux.
“I visited WSP in Ottawa several times throughout the project to go over sizes and options to ensure we had the precise solution for this project and then visited the jobsite as work progressed to ensure everything was arriving as it was specified and we could resolve any issues quickly,” said Pete Isaak with Oldcastle BuildingEnvelope.
The project also required higher span fixed windows for the penthouse units where sizes were different. The design team opted for the 1200 Arctic Wall Fixed windows for the application. OBE’s 2000 Arctic Operable Vents and MS-375 TC doors for the penthouse worked to provide residents with access to fresh air and natural light to complete the project.
Older buildings often come with various challenges on window replacement projects. From style – many used sliders in sizes that are not common today – to size requirements to performance limitations (often based on size and style requirements). A wide portfolio of solutions that can be adapted and modified is an important requirement for a window manufacturer to provide viable alternatives and flexibility to the design team. A consultative approach to help support the design process is the other requirement that can make the project move quickly and smoothly through the various phases of design and construction.
“Pete was available throughout the project, from helping in the design phase to supporting during issues and joining on job sites as well. We’ve worked with Pete and OBE on several other projects like this as well” Caux noted.
“We’ve always had good experiences with OBE. Pete is super responsive – you call, and he picks up the phone,” added Westwell. “He’s always looking out for us.”
“We were satisfied with how everything went. The condo management team was happy with the installation, how everything came together and how it looks,” added Caux.
With some creativity, flexibility and a range of solutions to select from, the design and construction teams delivered the window replacement project in a little over one year, meeting the requirements of the condo board, minimizing impact to occupants and delivering high performance windows to help residents save energy, and money, for years to come.
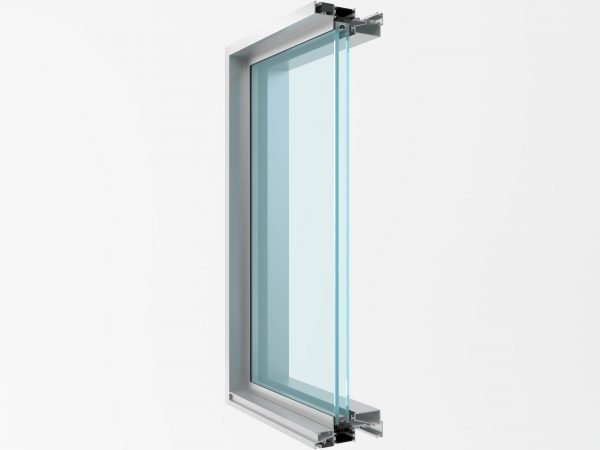
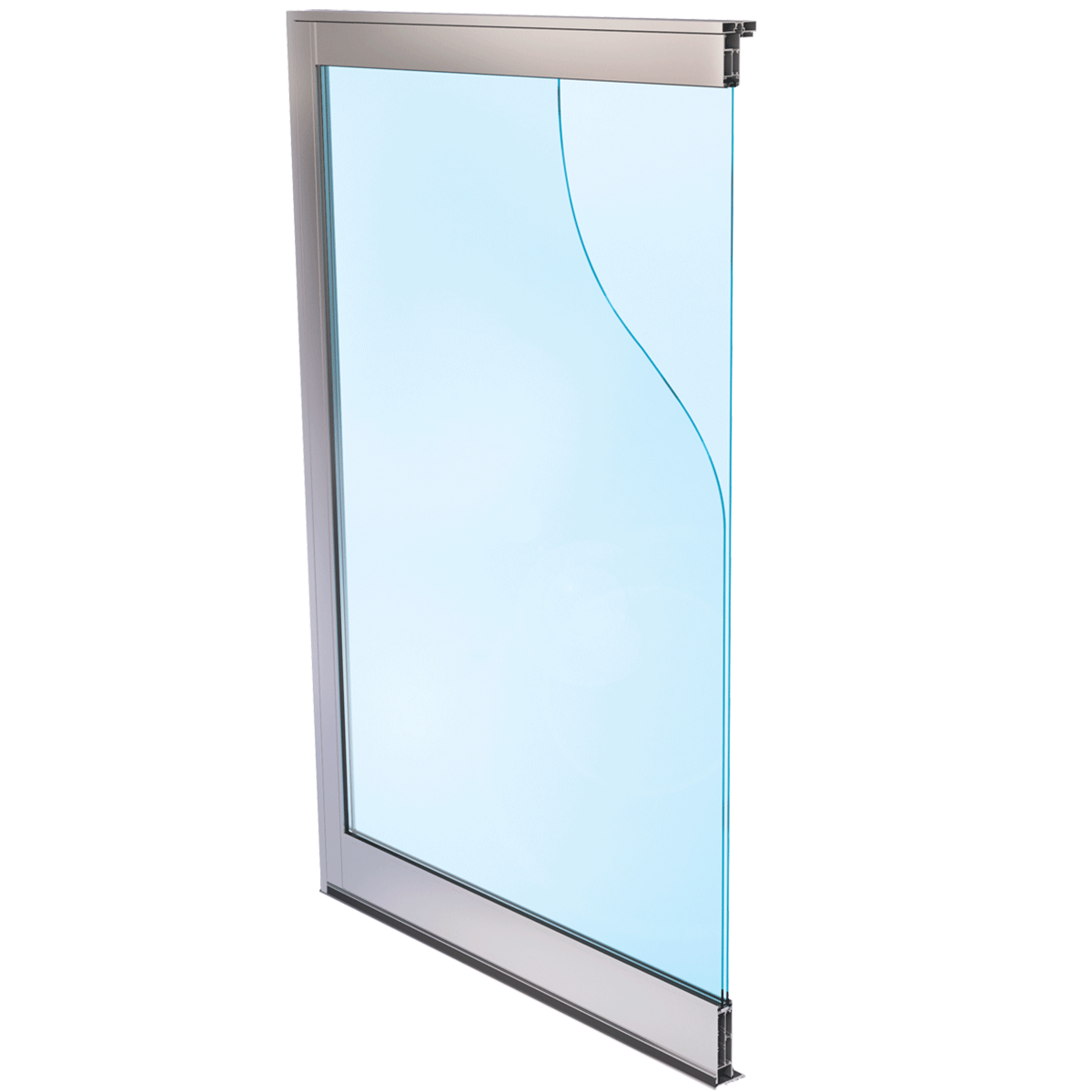